Common mistakes when managing inventories and how to avoid them
The inventory management is one of the most critical tasks in any business, as it directly affects the availability of products, customer satisfaction, and profitability. However, despite its importance, it is common for companies to make mistakes in this process, which can lead to significant losses. In this article, we will explore some of the most common errors in inventory management and how to avoid them to ensure an efficient and profitable operation.
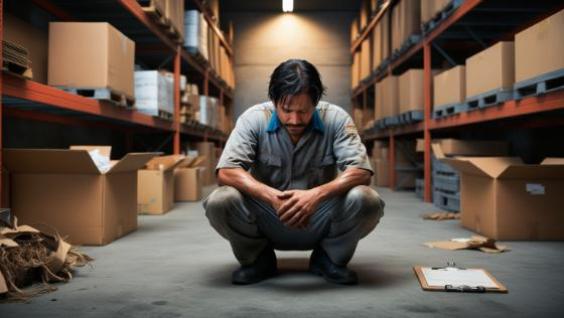
1. Lack of precision in inventory records
The error: One of the most common problems is the lack of precision in inventory records. This can be due to incorrect manual recording, not updating data in real-time, or the lack of an automated system. The imprecision in inventory can lead to overproduction, excess stock, or the lack of necessary products, affecting both operational efficiency and company finances.
How to avoid it: Implementing an inventory software that automates the update of records and ensures that each entry and exit of products is recorded with precision in real-time is fundamental. Solutions like Inventories1A allow for a detailed control of stock, avoiding manual errors and ensuring that inventory information is always up-to-date.
2. Not performing periodic physical counts
The error: Relying solely on digital records without performing periodic physical counts is a common error. Digital records may not always reflect reality, especially if there are losses due to theft, errors in recording entries and exits, or damaged products.
How to avoid it: Establishing a regular program of physical inventory counts, known as cyclic inventory, is essential. These counts should be compared with digital records to identify and correct discrepancies. An inventory software can facilitate this process, allowing for precise accounting adjustments when necessary.
3. Poor demand planning
The error: Underestimating or overestimating demand is another common error that can lead to excess stock or the lack of products. Both scenarios are costly: excess inventory immobilizes capital and can lead to product obsolescence, while the lack of stock can result in lost sales and dissatisfied customers.
How to avoid it: Using data analysis tools to predict demand with greater precision is key. Advanced inventory software, such as Inventories1A, offers features that allow for analyzing sales trends and consumption patterns, helping to plan purchases and adjust stock levels according to projected demand.
4. Not using a Kardex system
The error: Not having a Kardex system or not keeping it up-to-date is an error that can result in a lack of control over inventory. The Kardex is essential for having a detailed history of each product, recording all entries and exits.
How to avoid it: Implementing an inventory software that includes an automated Kardex system is the best way to ensure that all inventory movements are recorded and are accessible at any time. In Inventories1A, each product has a Kardex that is automatically updated with each movement, eliminating the need for manual records and ensuring the accuracy of inventory history.
5. Ignoring inventory rotation
The error: Not paying attention to inventory rotation can lead to problems such as the accumulation of obsolete or expired products. Products that are not sold quickly occupy space and capital that could be used more efficiently.
How to avoid it: Establishing policies for inventory rotation, such as the FIFO (First In, First Out) system, is crucial. This ensures that older products are sold first, reducing the possibility of obsolescence. Additionally, an inventory software can help identify low-rotation products, allowing for corrective measures to be taken in time.
6. Not integrating inventory with other management systems
The error: Managing inventory in isolation, without integration with sales, purchase, or accounting systems, can create inconsistencies and operational complications. This lack of integration can result in outdated data and decisions based on incomplete information.
How to avoid it: Implementing an inventory software that integrates with other platforms, such as Inventories1A, is essential for comprehensive business management. Our platform allows for synchronization with sales and accounting systems, ensuring that all areas of the company work with the same up-to-date information.
Avoiding these common errors in inventory management is essential to maintaining an efficient, profitable, and market-aligned operation. Precision in records, adequate demand planning, and the use of automated tools and integrated systems are key to achieving this.
Inventories1A offers a complete solution that helps companies avoid these errors, optimizing inventory management and ensuring that every aspect of inventory is under control, from Kardex to integration with e-commerce platforms.