Kardex: The key to precise inventory control in your warehouse
In the world of inventory management, the term "Kardex" is directly associated with a precise and detailed control of inventory. This system, which dates back to the first inventory accounting methods, remains an essential tool in modern warehouse management. In this article, we will explore what Kardex is, how it works, and why it is fundamental to maintaining an exact control of inventory in your warehouse.
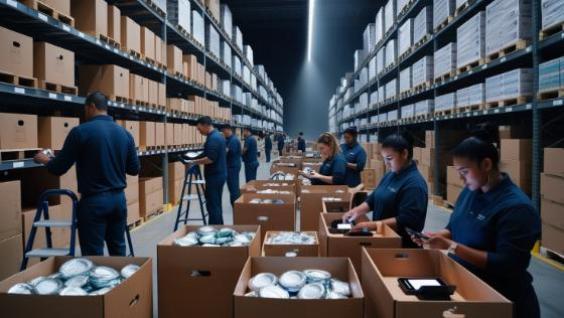
What is Kardex?
Kardex is a recording system that details all entries and exits of each product in a warehouse. Originally, it was kept on physical cards, where quantities that entered or left inventory were manually recorded. With the evolution of technology, Kardex has become part of inventory software systems, allowing for automated and real-time tracking of inventory.
How Kardex works in inventory management
The operation of Kardex is relatively simple but extremely effective. Every time a product enters or leaves the warehouse, this movement is recorded in the corresponding product's Kardex. This includes details such as the date of the transaction, quantity, current inventory balance, and any other relevant information, such as the supplier or destination of the products.
This continuous record allows companies to know at all times how many units they have of each product, facilitating informed decision-making about replenishment, distribution, and sales.
Benefits of using a Kardex system
- Accuracy in inventory control: By recording each inventory movement, Kardex ensures that inventory information is always accurate. This reduces the risk of human error and ensures that inventory decisions are based on reliable data.
- Detailed product history: Kardex acts as a complete history of each product in the warehouse. This is invaluable for conducting audits, tracking the origin of problems such as losses or damage, and understanding the product life cycle.
- Facilitates inventory rotation: With an updated Kardex, it is easy to implement inventory rotation strategies, such as the FIFO (First In, First Out) method, which ensures that the oldest products are sold first, avoiding obsolescence or expiration.
- Improves decision-making: Having an updated Kardex allows inventory managers to make informed decisions about purchases, sales, and storage. This is crucial for optimizing warehouse space usage and ensuring that there is always sufficient stock to meet demand.
Automated Kardex in modern inventory software
Today, Kardex has been completely digitized and integrated into advanced inventory software, such as Inventarios1A. Our system automates the Kardex recording process, eliminating the need for manual entries and ensuring that each inventory movement is recorded in real-time. This not only saves time but also reduces the margin of error and provides an instant and accurate view of inventory status.
With Inventarios1A, every time a product enters or leaves the warehouse, its Kardex is automatically updated, ensuring that you always have access to an accurate and detailed record of your inventory. Additionally, our software allows generating inventory reports based on Kardex data, facilitating inventory management and analysis.
Kardex is, without a doubt, an essential tool for any company that wants to maintain precise control of its inventory. By adopting an automated Kardex system like the one offered by Inventarios1A, you can significantly improve the accuracy of your records, optimize inventory rotation, and make more informed decisions that drive operational efficiency in your warehouse.
Don't let inventory management errors affect your business. Implement a robust Kardex system and ensure total control of your inventory.