Inventories: FIFO and LIFO Methods in Real Life
In the world of inventory management, FIFO (First In, First Out) and LIFO (Last In, First Out) methods are crucial concepts that determine how products are valued when they leave the warehouse. Although these methods are widely used in theory, their practical application in real life can be more complicated, especially when it comes to indistinguishable products and the lack of a batch system. In this article, we will explore how these methods are applied in real life and the challenges associated with them.
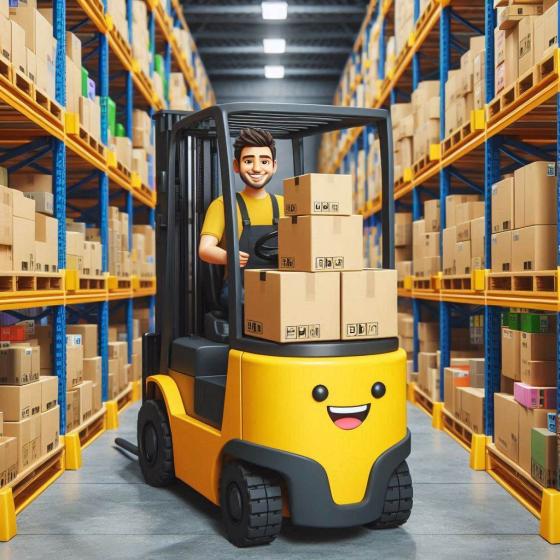
FIFO and LIFO: Basic Definition
- FIFO (First In, First Out): This method assumes that the first products to enter the inventory are the first to leave. That is, the oldest products are sold first. FIFO is useful for perishable products and situations where the acquisition date is important for valuation.
- LIFO (Last In, First Out): In contrast, LIFO assumes that the last products to enter the inventory are the first to leave. This method is less intuitive but can be useful in situations of inflation, as the most recent costs are used to value sales.
Application in Indistinguishable Products
In practice, applying FIFO and LIFO becomes challenging when products are indistinguishable and batch systems are not used. Let's consider the following example:
Example: Suppose you have beers purchased in January for $90 each and others purchased in February for $100 each. All the beers are of the same type and brand, without any unique identifier or batch code.
FIFO/LIFO Challenge: In a warehouse without physical separation or clear labeling, how do you decide if a sold beer comes from the January or February batch? The reality is that, without an adequate system, the warehouse worker might simply take the most accessible beer, and the FIFO or LIFO method becomes theoretical.
Solutions and Strategies
To overcome these challenges and effectively apply FIFO or LIFO, consider the following strategies:
Physical Organization of the Warehouse:
- Separation: Keep products from different purchase dates in separate areas of the warehouse. For example, organize January products in one section and February products in another. This facilitates the application of FIFO or LIFO.
- Labeling: Use visible labels to identify the acquisition date of each product. This helps ensure that the warehouse worker can follow the correct method when selecting products for sale.
Implementation of Batch Systems:
- Batch Registration: If possible, implement a batch system or unique codes for each purchase. This allows for precise traceability and facilitates the application of FIFO and LIFO.
- Inventory Management Software: Use inventory management software that allows you to register and track batches. This ensures that product exits are recorded according to the chosen valuation method.
Clear Operating Procedures:
- Training: Train warehouse workers on the importance of FIFO and LIFO and how to apply them correctly. Ensure they understand how to choose products according to the valuation method.
- Storage Policies: Establish clear policies for product selection and handling in the warehouse. This helps maintain organization and ensures that the correct valuation method is followed.
- Automation: Consider automation in inventory registration and tracking to improve accuracy in applying FIFO or LIFO.
- Integration: Ensure that sales software and inventory systems are integrated to maintain an accurate record of product exits.
The application of FIFO and LIFO in real life can be complicated when products are indistinguishable and batch systems are not used. However, with adequate warehouse organization, the use of labeling and batch systems, and the implementation of clear operating procedures, it is possible to effectively apply these methods. Technology and automation also play a crucial role in improving inventory management and ensuring accurate valuation. Adapting these strategies to the specific needs of your business can help you overcome challenges and manage your inventory more efficiently.